Renovation Planning During a Pandemic: Lessons from the Front Lines
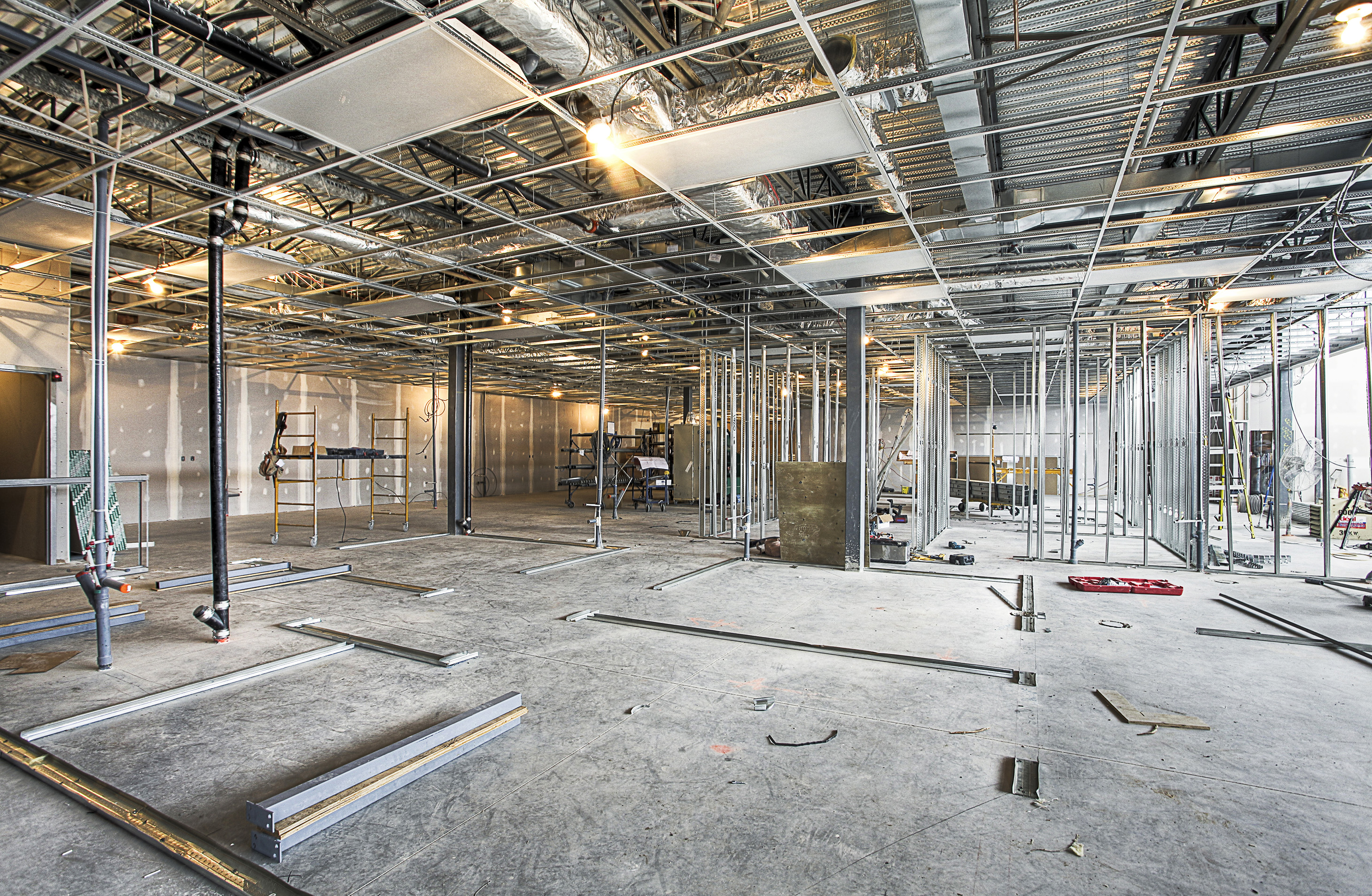
As a building owner, the choices you make during a renovation project can improve the health of your building and protect the health of its occupants. Your decisions can also give tenants the confidence they need to reoccupy and resume their lives. Your choices can not only solve short-term problems but provide lasting benefits.
As the head of an engineering firm specializing in Mechanical, Engineering and Plumbing (MEP) and fire protection, I like to speak with clients to understand their needs and concerns. And over the past few weeks, I’ve heard more than one client ask how they can adjust their renovation planning to limit the spread of the coronavirus.
Fortunately for building owners and MEP firms alike, the American Society of Heating, Refrigerating and Air-Conditioning Engineers (ASHRAE) is a fantastic resource. ASHRAE routinely publishes useful guidance on HVAC, building health, and safety issues—including the current pandemic.
ASHRAE’s guidance is based on the fact that properly configured HVAC systems can limit the transmission of infectious pathogens. In April 2020, the organization published position papers on various MEP best practices that can slow or reduce the transmission of airborne particulates. They share a list of recommendations from multiple perspectives, including safety, refrigeration, indoor air quality, and energy efficiency.
In this article, I want to discuss some of our clients’ concerns about the virus, and some of the ways we’re responding, which are partly informed by ASHRAE’s latest guidance.
Concerns and solutions
One of the most essential decisions an owner can make is in the amount of ventilation in their building. According to the prevailing theory, coronavirus spreads most often as an aerosol—tiny droplets that an infected person exhales. These infected droplets are then either inhaled by someone else or land on a surface that someone later touches.
One approach we can take is to design HVAC systems with greater ventilation rates—bringing in more outside air (typically only to a certain point during warmer times of the year), diluting aerosolized droplets, and minimizing the virus’ ability to spread.
Keep in mind, though, that achieving this result may not be simple. ASHRAE points out that “even the most robust HVAC system cannot control all airflows and completely prevent dissemination of an infectious aerosol or disease transmission by droplets or aerosols.” That being said, there are proven ways to increase the ability of your system to control the spread.
A related issue is filtration. For many buildings in the commercial market space, MERV 11 was a typical spec for filters in HVAC systems. At many government buildings, a rating of MERV 13 was more common. That means you have another option: to upgrade your filters to a higher MERV rating, allowing you to capture more particulates as they recirculate in your air conditioning system.
Another way to address the issue is to add equipment and controls to your HVAC system that maintain relative humidity (RH) at ideal levels. Studies have shown that a RH in the 40–60% range can reduce the spread of aerosols—and in the case of coronavirus, that is not an insignificant effect.
Installing ultraviolet germicidal radiation (UVGI) devices is another great option. We’ve already been talking with some of our institutional clients, including the GSA, about installing these devices on cooling coils to help take care of bacteria and fungi. These same devices also kill viruses, including the coronavirus.
Building owners should have a licensed mechanical engineer assess the conditions and capabilities of their systems before making any changes noted above.
An additional vector that likely spreads the coronavirus is infected surfaces— someone touches a surface containing the virus with their hands and then transfers the virus to their mouth, nose or eyes. This danger means that modifying the HVAC system alone is probably not enough. Contractors can help owners in other ways, too, including retrofitting buildings with touch-free fixtures, such as light switches, faucets, and toilets. While certain occupancy sensors are specified by code, some owners may want to look beyond those standards to maximize safety.
If the construction phase of your renovation project has not begun—even if you are late in the renovation planning stage—it’s probably not be too late to talk with your MEP engineering team about adding design features that could limit the spread of the coronavirus. You could also ask your contractor whether the delivery schedule could be expedited, given that during the pandemic contractors have easier access to the worksite and can work far more efficiently. Many firms now have robust teleworking capabilities that did not previously exist. For those buildings that are currently occupied, owners should evaluate if their staff are able to telework during some if not all of the renovation, resulting in faster and lower cost renovations.
Looking down the road
Just as sustainability features and LEED certification remain highly popular with owners and tenants years later, we expect virus-control features to have similar long-term appeal in the office building market moving forward—at least for the next two years, and perhaps longer.
As important as these adaptations are in improving the health and safety of building occupants, no one is certain what the future holds. The unknowns include when a vaccine and widespread testing will be available, how quickly and to what extent tenants and office workers return to their buildings, and how social distancing guidelines evolve over the coming years.
Jim Hoffman, PE, LEED AP O+M, CEM is president of Summer Consultants and has over 30 years of engineering design experience, both professionally and during his service in the U.S. Army as a combat engineer. He is involved in all facets of the company and works closely with team members on clients’ projects. He is also highly involved with complex renovations of HVAC systems, automatic temperature control systems, and chiller plants. His expertise spans federal, institutional, and historic facilities.
VIsit Summer Consultant’s Project Portfolio to view examples of our work.
Comments